Home construction with “printers” begins to be introduced
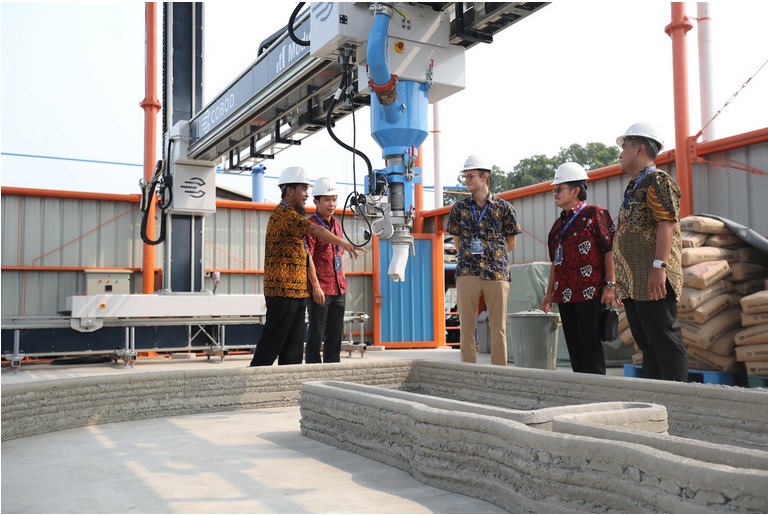
Source : Kompas.id | 23 May 2024
This construction technology is claimed to be able to build a simple house in 5 days and have a labor efficiency of 35 percent.
Building construction technology using three-dimensional printing or printer methods is starting to be introduced in Indonesia. This construction technology is claimed to be able to build a simple house in 5 days with labor efficiency of up to 35 percent.
PT Modula Tiga Dimensi, a joint venture company of PT Bakrie & Brothers Tbk (BNBR) and Cobod International from Denmark, has started working on the three-dimensional printing construction industry or 3D construction printing (3DCP). It is claimed that making building walls using a printer can save construction time, labor and use more environmentally friendly materials.
Operational Director of PT Modula Tiga Dimensi (Modula) Debiyarto Imran, stated that three-dimensional printed construction is a disruptive technology in the field of building construction. The construction of buildings, such as houses, buildings and bridges, is made using a printer mechanism. Instead of making building walls by installing bricks, walls are now simply printed with a printer.
The use of three-dimensional printing construction technology is considered to save time for building a house. As an illustration, if installing bricks for a 45 square meter residence (type 45) takes 1.5 months, then with the printer mechanism it can be completed in five days.
”We partner with Cobod International. We brought in printer units, so we claim to be pioneers in the 3D construction printing industry. “The use of this (technology) is already moving in developed countries, so the trend is going there,” said Debiyarto, when contacted, Thursday (23/5/2024).
Apart from Cobod International, other companies that apply three-dimensional printing technology include Black Buffalo 3D, as well as Icon from the United States, Cybe 3D from the Netherlands, and Apis Cor 3D from Russia. Cobod International, for example, has nearly 80 printer machines for the application of three-dimensional printing construction throughout the world.
Debiyarto added that these building materials, which have a composition of sand, aggregate (stone) and cement, are considered more environmentally friendly and can rely entirely on domestic material sources. Currently, many green cement products are considered to be produced in Indonesia.
Home Shortage
Debiyarto said that his party plans to build a pilot residence using three-dimensional printing construction technology starting this year. Apart from that, his party is also reviewing the construction of buildings using this technology for upper segment, middle segment and row houses. For the initial stage, residential products will be marketed to the upper middle segment of society.
His party is also ready to study the use of similar technology for middle segment houses with building costs of IDR 5 million per square meter (m2), down to the simple house segment. His party will also collaborate with the Ministry of Public Works and Public Housing to apply this construction to residential building standards, as well as carry out tests for earthquake-prone areas.
“Gradually, we will also review procurement for the lower middle segment by adjusting finishing materials. “We will try to focus and enter this segment,” he said.
One of the houses with earthquake-resistant specifications is seen which is currently under construction in Wani Satu Village, Tanantovea District, Donggala Regency, Central Sulawesi, Wednesday (19/2/2020).
Previously, Modula President Director Adi Bagus Tirto said that the housing market in Indonesia was still experiencing a supply shortage. The need for livable houses in Indonesia reaches around 600,000-800,000 units per year. However, the available supply is only 400,000-500,000 units per year. It is estimated that 30 million households in Indonesia will need adequate housing by 2030.
Director & Chief Financial Officer (CFO) of PT Bakrie & Brothers Tbk, Roy Hendrajanto M Sakti, in a press statement on Tuesday (21/5) stated that the environmentally friendly three-dimensional printing construction technology is expected to be able to overcome the shortage of houses in Indonesia, especially in the construction segment buildings and housing. In addition, it is in line with environmental, social and governance (ESG) principles.
“We see that the potential for growth of this industry in Indonesia is very large. “This is a business opportunity that is worth exploring and developing,” said Roy, who is also the President Commissioner of Modula.
Co-Founder & Head of Asia-Pacific Cobod International, Simon Klint Bergh, also in a press statement on Tuesday, said that three-dimensional printing construction technology focuses on solutions to the problem of housing shortages by adhering to sustainable and environmentally friendly principles. This technology is considered capable of building houses smarter, faster, more sustainably and energy efficient, thus becoming a solution for construction in Indonesia.
“This technology reduces more than 50 percent of the time required for conventional house construction, saves 35 percent of labor, saves material residue disposal by up to 20 percent and provides design flexibility and high precision,” he said.
Chairman of the Indonesian Precast and Prestress Expert Association (IAPPI) Hari Nugraha Nurjaman, when contacted Thursday (23/5/2024), stated that three-dimensional printing construction technology is still in the pilot stage. Therefore, technically it still needs an earthquake resistance test. “The cost aspect also needs to be studied. “If studies and trials continue to be carried out, it will become clearer the market position for this technology,” he said.